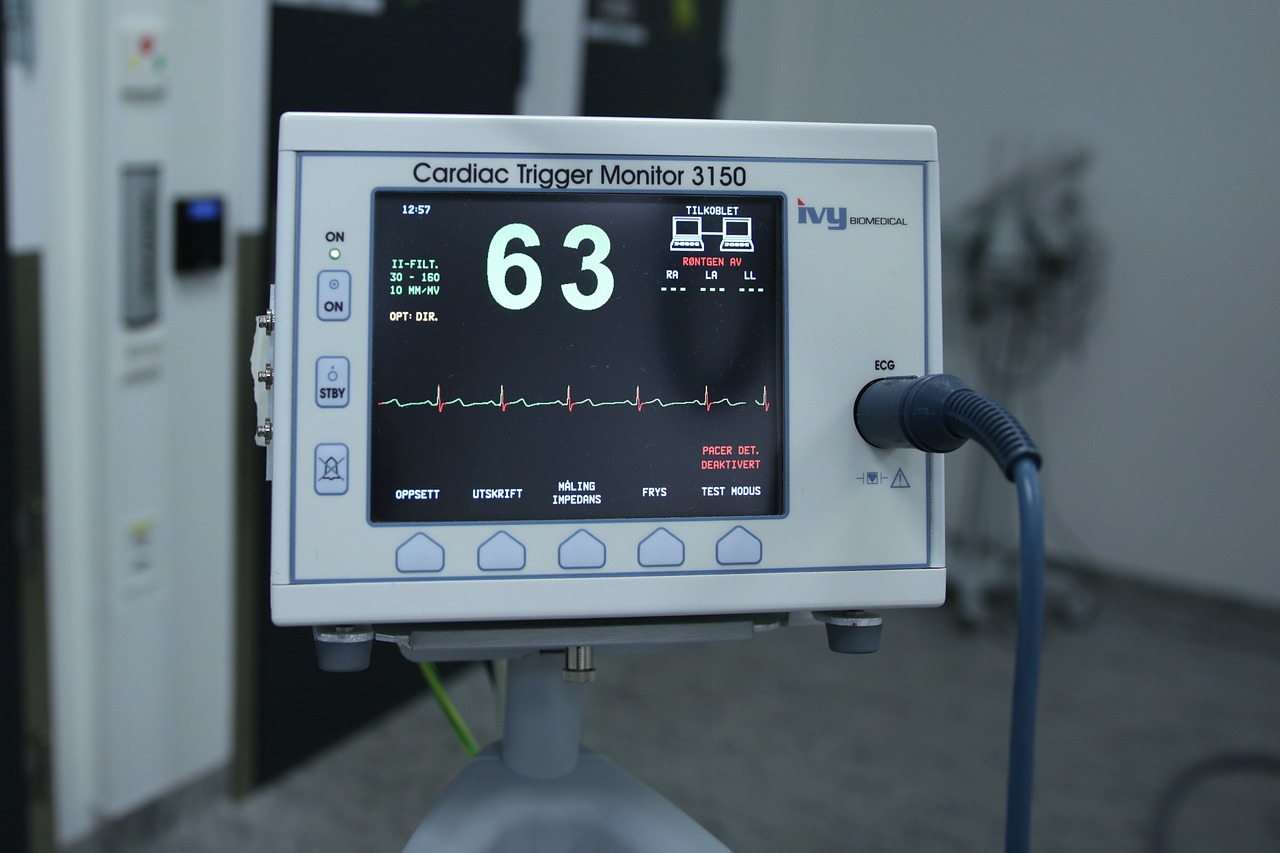

Introduction to Biocompatibility in Medical Implants
Medical implants have converted cutting-edge healthcare, supplying solutions for changing or assisting broken organic systems in the body, from orthopedic implants to dental prosthetics. A key consideration for the success of those gadgets is biocompatibility, which refers to an implant’s capability to carry out its characteristic with out triggering harmful immune responses within the body. Biocompatibility guarantees that substances do no longer cause toxic reactions, inflammation, or other unfavourable responses, making it vital for patient safety and the lengthy-time period achievement of implants.
Historically, implant biocompatibility has been an ongoing venture, as early materials like metallic regularly brought on detrimental reactions due to their loss of compatibility with frame tissues. Today, powder metallurgy is emerging as a innovative approach to enhance the biocompatibility of implants, permitting the best design of substances at micro and nano tiers. This technique is assisting cope with compatibility demanding situations, as a result improving the effectiveness and safety of clinical implants.
Enhanced Customization with Powder Metallurgy Parts
One of the most big advancements in the usage of powder metallurgy for medical implants is its ability for custom designed component manufacturing. Powder metallurgy elements may be designed to meet the precise anatomical and physiological necessities of each affected person. This approach enables changes in geometry, porosity, and floor texture, growing parts that better combine with surrounding tissues. This customization allows reduce the want for extra surgical procedures, as implants can be tailored for premiere healthy and feature. Additionally, powder metallurgy elements allow for customized functions like bone growth channels, which sell natural tissue integration and decorate long-term balance.
Integration of Bioactive Agents in Powder Metallurgy Parts
The use of bioactive agents within powder metallurgy parts is an innovative approach to further improve implant biocompatibility. By incorporating substances such as antimicrobial nanoparticles or growth factors directly into the powdered material, implants can actively contribute to healing and reduce infection risks. These bioactive powder metallurgy parts release agents that help inhibit bacterial growth or stimulate tissue regeneration. This functionality not only strengthens the initial integration of implants but also supports long-term health outcomes by reducing postoperative complications and promoting tissue bonding.
Advanced Applications of Metal Injection Molding (MIM) Parts in Implant Production
Metal Injection Molding (MIM) is another powder metallurgy technique with promising applications for medical implants, allowing for the production of highly complex shapes and detailed features on a miniature scale. By using MIM, manufacturers can create intricate parts that meet the precise specifications required for small, durable, and biocompatible implant components. MIM parts are especially valuable in orthopedic and dental applications, where small, complex geometries enhance the functionality and fit of implants. This method also supports the use of biocompatible alloys, such as titanium and cobalt-chromium, which exhibit excellent strength and corrosion resistance, making them ideal for long-term implants.
Challenges in Biocompatibility
Implant biocompatibility challenges can stem from various factors, such as the chemical composition, surface properties, and physical characteristics of the material. Typical issues include inflammation, toxicity, and potential rejection by the body’s immune system. For example, metal implants can corrode over time, releasing ions that lead to inflammatory responses and even metal allergies in sensitive individuals. Biofilm formation is another issue, where bacterial colonies form on implant surfaces, risking infection.
The development of biocompatible materials is rooted in a historical pursuit of materials that reduce immune rejection and adverse responses. Metals like titanium have shown significant improvements over earlier materials due to their passivating oxide layer, which limits corrosion and minimizes the risk of inflammatory responses. However, there remains a need for enhanced surface properties to support cellular integration and minimize infection risks.
Fundamentals of powder metallurgy
Powder metallurgy is a process in which fine metal powders are aggregated and heated (or sintered) to produce solid, homogeneous materials. This process differs from traditional methods of metallurgy such as casting or forging, which involve melting and can lead to unwanted corrections and structural abnormalities Powder metallurgy offers unique advantages over in the control of material systems and the acquisition of complex designs accurately.
Traditional metal processing often requires high temperatures and sophisticated mechanical processes, which can reduce implant structural uniformity and compatibility with biomaterials in the meeting on the. In contrast, powder metallurgy allows careful control of porosity, density, and surface roughness—all factors necessary to enhance biocompatibility in implants Powder metallurgy’s ability to produce highly controlled microstructures and surface properties idealize medical implants that need to integrate seamlessly with biological tissues
Powder metallurgy techniques for pharmaceutical implants
Sintering is an important step in powder metallurgy, where powdered materials are heated to temperatures below their melting point, causing the particles to aggregate without acquiring a liquid state This process increases the hardness and mechanical strength increases, resulting in stability. The durability is important for implants, as high-strength metals can withstand mechanical loads in the human body without excessive deformation
Surface enhancement methods
Surface properties, such as textures and coatings, play an important role in biocompatibility. Powder metallurgy allows for the design of the bone surface, promoting bone growth and helping to better secure implants. Furthermore, biocompatible coatings such as hydroxyapatite can be applied to metal surfaces to improve integration with the surrounding tissue. Additive matter, a form of powder metallurgy, allows for precise control of surface roughness and texture, which is essential for cell function and reduces the risk of infection
Materials Selection for Improved Biocompatibility
Overview of Commonly Used Materials
Materials like titanium and zirconium are widely utilized in powder metallurgy for clinical implants. Titanium is known for its power, light-weight, and first-rate biocompatibility due to its herbal oxide layer that resists corrosion. Zirconium offers comparable benefits, with delivered resistance to wear, making it a perfect preference for joint replacements and other high-pressure implants. These metals, while processed through powder metallurgy, can acquire most fulfilling surface systems for higher integration with frame tissues.
Novel Materials and Composites Developed Through Powder Metallurgy
Powder metallurgy enables the advent of composite materials that combine the strengths of different metals, ceramics, and polymers. For instance, titanium-tantalum alloys provide advanced corrosion resistance and biocompatibility, even as also providing mechanical strength. Bioceramics like hydroxyapatite can be added to metal matrices, creating a hybrid structure that encourages bone increase and gives higher implant stability. Innovations in powder metallurgy allow for custom compositions, giving medical professionals extra options for tailor-made implant materials.
Conclusion
Improving biocompatibility in medical implants is essential for patient safety, comfort, and recovery outcomes. Powder metallurgy stands out as a powerful method to design and fabricate implants that integrate well with biological tissues. By enabling precise control over material properties—such as density, surface roughness, and porosity—powder metallurgy techniques offer enhanced implant performance and a promising solution to traditional biocompatibility challenges. Advances in materials science, combined with powder metallurgy, point toward a future where medical implants can be customized for each patient, reducing complications and improving the overall quality of life.